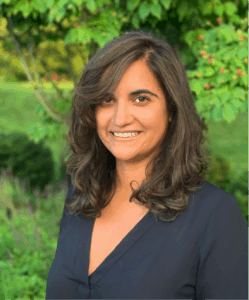
Sonia Alreja is the Operations head for VJ X-Ray. She received her undergraduate degree in Economics from New York University in 2010. She started her career working in politics for a US Congressman and a lobbying firm focusing on energy production. Since 2014, she has worked in growing the VJX team and customer base. Today with over 50,000 units the field, VJ X-Ray is a global leader in complete x-ray sources and high voltage generators specializing in the security inspection field and food quality.
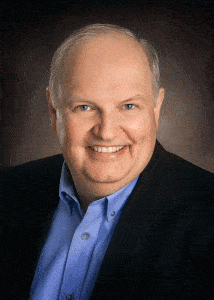
Dr. Kevin Anderson is Senior Technical Fellow for Brunswick Corporation, Mercury Marine Division, located in Fond Du Lac, Wisconsin. He is responsible for both materials research and applications across the corporation. Previously, he was leader of aircraft materials and physical metallurgy at Reynolds Aluminum Research. He received his B.S., M.S., and Ph.D. degrees in metallurgical engineering from the University of Illinois at Urbana – Champaign. He is a fellow of ASM and a member of The U.S. National Academy of Engineering (NAE) for his work on sustainable aluminum alloy design. He is also inventor of high damage tolerant diecasting alloys that are made from 100% recycled aluminum and are registered with the Aluminum Association. In addition to receiving several important industrial awards, Dr. Anderson holds over 30 United States patents with the vast majority successfully in production. He has taught aluminum metallurgy on an international level since 1999, is a member of the U.S. National Materials and Manufacturing Board, a member of the Aluminum Association Technical Committee on Product Standards and Subcommittee on Alloy and Temper Registration, vice chairman of the peer committee of the materials section of the NAE, and is a member of the Grainger Institute for Engineering Advisory Board at the University of Wisconsin. He is past chairman of both the Advanced Casting Research Consortium and TMS’ Materials Innovation Committee. Locally, Dr. Anderson is the founding president of the Fond Du Lac STEM Academy and Fond Du Lac STEM Institute, which are public charter schools for students in grades 3-5 and 6-12, respectively.

Rodney Wirtz is a Mechanical Engineer with over 20 years at Almex and has previously worked for Alcoa and Kaiser Aluminum. He has a Mechanical Engineering Master’s degree from Long Beach State University and has significantly contributed to Almex’s mission as the Engineering Manager. He oversees the development of Almex’s systems, including melting furnaces, casting systems, homogenization furnaces, control and SCADA systems. He is a registered Mechanical Engineer in the State of California.
AlmexUSA, Inc. is an industry leader in wrought aluminum alloy casting systems and produces many aluminum alloys.
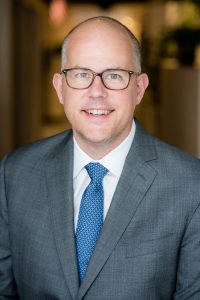
Jason T. Sebastian, Ph.D. is QuesTek’s President focusing on overall company growth and management, and on the entire spectrum of commercial- and government-sponsored alloy modeling, development, and deployment activities. He is a specialist in the fields of alloy development and commercialization, computational materials design, and nanostructural materials characterization. Since joining QuesTek in 2006, his work has focused on: the development of high strength steels for structural and power transmission applications; precipitation-strengthened cobalt-based alloys; alloys for additive manufacturing; non-toxic, high-strength/low-friction copper-based alloys to replace lead-containing bronzes; a low-cost, castable titanium alloy; a highly-processable nickel-based superalloy; advanced soft magnetic alloys; and other computationally-designed alloys.

Victor Khristov is the CEO / Owner of CPC Europe. He received his degree in International Business from Boston University in 1999. Since then he has worked strictly in the Automotive Aluminum casting Field. His focus is on brining the Counter-Pressure Casting Technology to new frontiers of light weight automotive parts. Including chassis, knuckles, control arms, hybrid brake disc’s, furl cells, calipers, RUB, torque boxes, and subframes both hollow and solid.
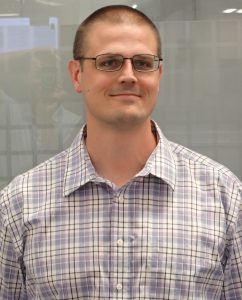
Ryan Breneman, Ph.D. is Discipline Chief for Castings at Pratt & Whitney’s development single-crystal foundry. In this role he works to develop new casting technologies for emerging applications and produce development castings for experimental test engines. Ryan has been awarded 20 US patents at Pratt & Whitney and authored several publications in his former life as a ceramist. While primary focus is on single-crystal, nickel-superalloy, he also works in aluminum and other light alloys. Research interests include incorporating additive and digital tools to push the limits of casting technology.
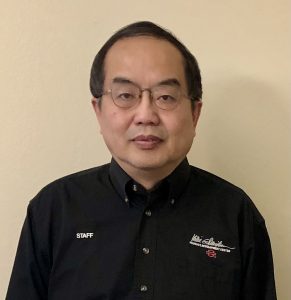
John Jiang, PhD of metallurgical engineering, is senior materials engineer at Harley-Davidson product development center since 2006. John’s responsibility is on lightweight (Al and Mg) component development. Prior to joining HD, John worked for the die casting industry for 10 years. John’s passion is in casting, forging, alloy development and failure analysis.
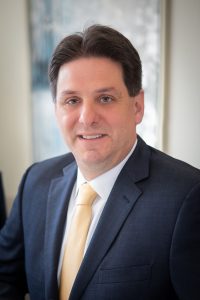
Uli Blankenstein Vice President Strategy and Execution at Materion Corporation, is responsible for the development and implementation of market, technology and operations growth strategies of the Electronic Material Division. He has worked in the technology metals business all of his career specializing in Physical Vapor Deposition materials and Specialty chemicals. He has been focused on the manufacturability of complex precious and specialty metal alloys needed in leading edge Semiconductor manufacturing. He is responsible for manufacturing facilities throughout North America as well as Europe, China, Taiwan, Korea, Singapore and Malaysia.
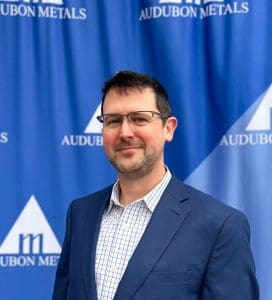
Matthew Gavin is the Senior Metallurgist at Audubon Metals. Working with suppliers, customers, research consortia and academia, Matthew is leading Audubon’s efforts in developing and commercializing new products and improving manufacturing processes. Prior to Audubon Metals, Matthew spent 15 years in primary aluminum specializing in extrusion billet and sheet casting in a variety of technical and manufacturing roles.